Новолипецкий ренессанс промышленной экологии
Как стремление к наилучшим стандартам охраны окружающей среды меняет металлургию в России
Фото: НЛМК
Фото: НЛМК
С тех пор, как в правительстве России заговорили о промышленной экологической политике на основе наилучших доступных технологий (НДТ), прошло 15 лет. На примере металлургической отрасли можно судить, каких результатов можно добиться, опираясь на лучшую практику и комплексную политику охраны окружающей среды.
Группа НЛМК к 2023 году сократила эмиссию до уровня НДТ ЕС, снизила в два раза стоки в водные объекты и переработала более 99% вторичного сырья.
Ответственное отношение к окружающей среде является ключевым приоритетом компании на протяжении уже более 20 лет. С 2000 года НЛМК инвестировал в экологическую модернизацию порядка 127 млрд руб., выделив экологическое направление в отдельную функцию с собственной стратегией и целеполаганием. В реализации своей экологической программы НЛМК ориентируется на наилучшие доступные технологии и лучшие практики в отрасли.
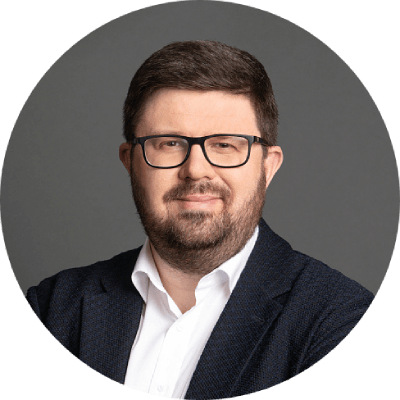
Соответствие наилучшим доступным экологическим технологиям — это один из ключевых критериев для принятия решений при реализации любого инвестиционного проекта. Такой подход сделал экологическую повестку частью ДНК компании, ее технологической культуры. Для меня лично, как для человека, для которого Липецк является родным городом, это очень важно. Наши производственные площадки являются неотъемлемой частью городов присутствия, а наши сотрудники и их семьи — жители этих городов. Мне сложно представить, как можно было бы по-другому выстраивать экологическую стратегию компании. Наша задача как менеджмента — минимизировать воздействие промышленных объектов на окружающую среду, в том числе за счет внедрения НДТ в каждом производственном процессе.
Компания также активно использует возможности цифровизации для экологических целей: ведет мониторинг эмиссии при помощи машинного зрения, оснащает датчиками мониторинга не только свои производства, но и города присутствия, чтобы следить за экологической ситуацией комплексно. Результаты измерений можно увидеть онлайн — на сайте компании. На ключевой площадке группы — в Липецке — видеокамеры охватывают 100% основных источников эмиссии. Данные с них поступают в ситуационный центр, где за ними следят операторы, в том числе для быстрого реагирования на возможные отклонения.
Единая система экологического видеомониторинга и контроля охватывает и крупные очистные сооружения. Например, на биохимической очистке воды коксохимического производства стоит десять камер, информация с которых поступает к технологам. Кроме того, в 2024 году группа НЛМК начала оснащение источников эмиссии средствами автоматизированного контроля, которые позволят регулятору и другим заинтересованным сторонам получать доступ к экологическим данным компании онлайн.
Воздух
Контроль за эмиссией в атмосферный воздух — один из главных приоритетов в экологическом управлении НЛМК. Затраты на охрану атмосферы составляют более половины всех расходов компании на охрану окружающей среды.
В НЛМК подчеркивают, что даже при значительном росте производства компания не просто не увеличила, а сократила экологическое воздействие, снижая и абсолютные, и относительные показатели эмиссии. С 2000 года валовая эмиссия компании в атмосферный воздух сократилась на 18% при росте производства стали в два раза. Удельный показатель снизился за это время в 2,5 раза.
Задача НЛМК — не просто снизить объем эмиссии, но улучшить качество воздуха, которым дышат люди. Пример такого подхода — программа по исключению запаха сероводорода от источников комбината в Липецке. Несмотря на то что превышений нормативов по эмиссии сероводорода у НЛМК не фиксируется, до 2024 года комбинат оставался источником неприятного запаха, который появляется даже при минимальных концентрациях вещества в атмосфере. Чтобы исключить запах сероводорода от источников комбината, компания с 2015 года вложила более 10 млрд руб. в реконструкцию своих производств — от коксохимического цеха до переработки доменного щебня.
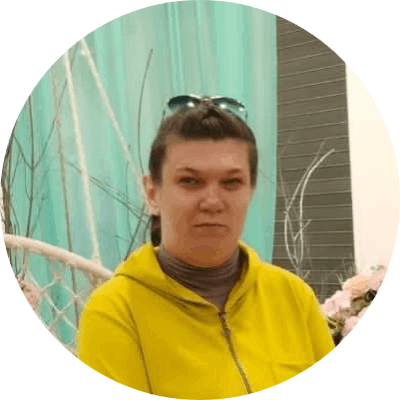
Я всю жизнь живу в районе Тракторного завода, этот район Липецка близко к очистным и некоторым площадкам НЛМК. Раньше он славился запахом сероводорода, и, действительно, к вечеру у нас постоянно усиливался неприятный запах. Летом в жару это было вообще невыносимо, мы даже закрывали окна. Сейчас его нет. Не помню, когда последний раз мы замечали этот запах. Дышим свободно, окна открыты, и особенно довольны изменением ситуации пожилые люди.
К аналогичным проектам относятся и мероприятия, которые компания с 2022 года реализует в рамках федеральной программы «Чистый воздух». Семь из них выполнены, еще два будут завершены до 2026 года, по итогам которого компания планирует сократить эмиссию на более чем 20% по отношению к 2017 году. Среди уже реализованных крупных проектов в рамках этой программы — капитальный ремонт газоочисток двух доменных печей, двух конвертеров (фактически половины производства комбината), строительство еще одного комплекса переработки доменного щебня. Сумма инвестиций в эти проекты превысила 100 млрд руб.
Реконструируя любое производство, НЛМК применяет самые современные технологии, которые превосходят установленные нормативные требования. Например, новое газоочистное оборудование способно улавливать 99,9% пыли в газах, отводимых в атмосферу, а остаточная запыленность после очистки составляет 5 мг на 1 кубометр воздуха, что в пять-шесть раз ниже, чем чистота воздуха после фильтрации в бытовых пылесосах.
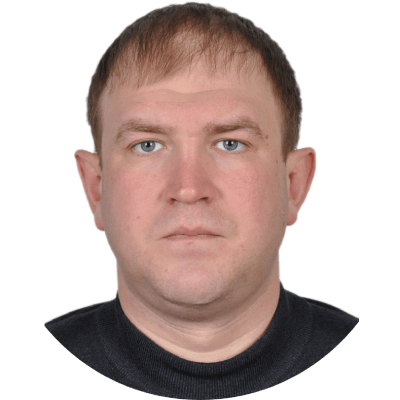
«В нашем цехе на протяжении нескольких лет модернизировалось оборудование для очистки воздуха, после проведенных реконструкций оборудования экологическая ситуация в цехе вышла на новый уровень. Например, теперь системы очистки в момент повалки конвертера и заливки чугуна забирают от 18 до 23 тонн пыли в сутки, все это раньше находилось в цехе. Теперь условия на рабочих местах стали гораздо лучше. Раньше при заливке чугуна в конвертер над кровлей цеха был рыжий дым. Сейчас такого нет — все собирается и утилизируется. На рабочих отметках оборудования гораздо меньше пыли. Лучше дышится.
Если раньше мы ходили по графиту и уборку надо было делать каждый день, то теперь ту же территорию можно убирать не чаще одного раза в две недели. И норма качества воздуха в цехе соответствует всем показателям.
Новое оборудование прошло испытания и подтвердило эффективность работы всех элементов газоочистки. Сокращение эмиссии пыли на участке благодаря проекту составило 94% — то есть пыли стало в 16 раз меньше.
Проведенная реконструкция стала первым шагом, позволившим спланировать и начать сбор и утилизацию газа сталеплавильного производства. Он накапливается в газгольдерах и будет использован для выработки электроэнергии на новой теплоэлектростанции, которая строится на НЛМК. Это будет первый в России проект использования конвертерного газа как топлива для выработки электроэнергии вместо его сжигания на факелах. Он позволит сократить эмиссию парниковых газов на 650 тыс. тонн и оксида углерода на 3 тыс. тонн.
Фото: НЛМК
Фото: НЛМК
Подобные проекты позволяют Липецку уже на протяжении девяти лет сохранять низкий уровень загрязнения атмосферы, удерживая статус самого чистого металлургического города — по качеству воздуха он сопоставим с городами, где нет крупных объектов промышленности. Доказательством этого являются данные экологического мониторинга не только самой компании, но и независимых лабораторий Росприроднадзора, Роспотребнадзора и Гидромета. Всего компания ежегодно получает и анализирует данные по 30 веществам в 950 точках на заводе и в городе — это 4 млн замеров в год, или порядка 8 замеров каждую минуту.
Вторсырье
Отходы группы возвращаются в производственный процесс практически в полном объеме: на сторонние полигоны направляется лишь 0,1% от общего объема — в основном это твердые бытовые отходы.
За последние 20 лет удельное образование отходов по группе в целом сократилось в семь раз, несмотря на рост производства вдвое.
Следуя лучшим практикам, стратегия компании по обращению с вторичным сырьем направлена на минимизацию образования отходов, увеличение доли их переработки и повторного использования, которая уже превысила 99%.
Например, с 1934 года на шлаковом отвале накапливались различные вторичные продукты металлургического производства. Отвал занимал площадь 25 гектар, что эквивалентно 35 футбольным полям, с общим весом накопленных вторичных ресурсов 5 млн тонн, включая доменный шлак и другие виды железосодержащего вторсырья. Этот отвал полностью переработали в 2020 году. Десятую часть вторичных ресурсов в отвале составлял металлический лом разных фракций, который в процессе переработки был извлечен методом магнитной сепарации. Железо полностью вернули обратно в производство, а извлеченные щебень и строительные материалы использовали в дорожном строительстве и для сооружения комплекса безводного охлаждения доменного щебня на месте отвала.
Сегодня нового накопления вторсырья не происходит. Все железосодержащие продукты направляются в агломерационное производство и на фабрику брикетирования, после чего поступают в доменное производство. Не железосодержащее вторсырье — огнеупорные материалы, масла, строительный лом и другие — продаются для использования и переработки внешними компаниями. Сейчас также исследуется вопрос переработки древесных отходов в биоуголь.
Фабрика брикетирования — крупнейший проект НЛМК по переработке вторсырья стоимостью 5 млрд руб. Это фактически завод по переработке вторичных ресурсов, специально построенный внутри комбината. Сырье для фабрики приходит из доменного цеха, где при выплавке чугуна системами газоочистки улавливается железосодержащая пыль. Железо и углерод в составе позволяют применить ее повторно в производстве.
Фото: НЛМК
Фото: НЛМК
Специалисты НЛМК адаптировали метод экструзии (используется для производства, например, кирпичей) для разработки технологической линии, которая превращает пыль и шлам (это смесь пыли и воды) в сырье. Смесь из вторичных продуктов с добавлением железосодержащего концентрата и других компонентов перемешивают со связующим компонентом, после чего производят брикеты. Далее их используют в доменном производстве в качестве сырья.
Железо и углерод в брикетах позволяют снизить расход сырья и топлива в доменном производстве. За четыре года фабрика брикетирования вернула в производство более 700 тыс. тонн вторичных продуктов. Таким образом, формируется полноценный замкнутый цикл: системы газоочистки НЛМК эффективно улавливают пыль, очищая воздух, при этом уловленная пыль не отправляется на полигон, а используется повторно для производства все той же стали.
За счет эффективной работы по вовлечению вторичного сырья НЛМК ежегодно предотвращает отправку на полигоны около 20 млн тонн сырья — по объему это сопоставимо с составом поезда, который бы растянулся от Москвы до Красноярска — все это НЛМК повторно использует в производстве.
Вода
Группа НЛМК является лидером мировой металлургии по эффективному использованию воды в производстве и стремится к 2030 году полностью исключить воздействие на водные объекты за счет прекращения промышленных стоков и повторного использования водных ресурсов. Сегодня на предприятиях компании действуют 80 замкнутых водооборотных систем, а доля оборотного водоснабжения находится на стабильно высоком уровне — более 97% воды (3,2 млрд кубометров, что сопоставимо с объемом пяти Суэцких каналов) многократно используется после прохождения очистки на предприятиях группы. Остальные 2,5% поступают извне для компенсации испарившейся воды.
Хозяйственно-бытовые и промышленно-ливневые стоки на НЛМК разделены. Промышленные стоки компании находятся в замкнутом водообороте с 2009 года, и стока в поверхностные воды нет.
Все промышленно-ливневые стоки поступают в коллектор, а затем в пруды-отстойники, в которых происходит механическая очистка воды, тяжелая фракция оседает, и вода осветляется. Осветленная вода перекачивается потребителям комбината для повторного использования.
Примеров таких, аналогичных НЛМК, водооборотных систем в России немного. В 2009 году этот проект стоил предприятию 644 млн руб. Для запуска системы на комбинате провели масштабную модернизацию: построили новые насосные станции и сеть трубопроводов длиной 46 км, реконструировали действующие насосные станции, запустили новую технологию газоочисток, изменили схему доочистки воды и ее транспортировку к цехам. Все технические решения и обновленное технологическое оборудование соответствуют НДТ. Проект позволил компании снизить потребление речной воды вчетверо — с 71,3 млн в 2008 году до 18,6 млн кубометров в 2023 году, или чуть более 2 кубометров на тонну стали, что является одним из лучших показателей в мире.
Хозяйственно-бытовые стоки от столовых, санитарно-бытовых помещений, прачечных, душевых НЛМК поступают на локальные очистные сооружения (ЛОС). Применяемая технология очистки — с биологическим удалением азота и фосфора — соответствует НДТ. В 2021 году НЛМК провел модернизацию ЛОС, чтобы повысить эффективность очистки и улучшить качество хозбытовых стоков.
Фото: НЛМК
Фото: НЛМК
Теперь очищенная на ЛОС вода подходит для повторного использования на предприятии, и НЛМК планирует направить очищенные и обеззараженные стоки ЛОС в существующую систему водоснабжения комбината уже в 2025 году. Это уникальный для России проект. Он предполагает замещение речной воды в локальных водооборотных системах и организацию новой независимой схемы подачи очищенных хозяйственно-бытовых стоков.
В результате реализации проекта потребление речной воды сократится еще на треть, или на 6,5 млн кубометров в год, сток очищенных хозяйственно-бытовых вод комбината и части Левобережного района города Липецк в реку Воронеж будет полностью прекращен в конце 2024 года. Это также позволит сократить городские стоки Липецка на 15% — то есть компания будет повторно использовать не только свои вторичные ресурсы, но и вовлекать сточные воды жилых районов. Инвестиции в проект превысят 1 млрд руб., а НЛМК сохранит глобальное лидерство среди металлургических компаний в области защиты водных ресурсов.